Thin metal sheets with holes, commonly known as perforated metal sheets, are a versatile and indispensable product in various industries. These sheets are made by hand-punching or machine-pressing holes into thin metal, such as stainless steel, aluminum, or brass. The creation of these sheets may sound straightforward, but it requires remarkable precision and expertise to meet the specific requirements of different applications.
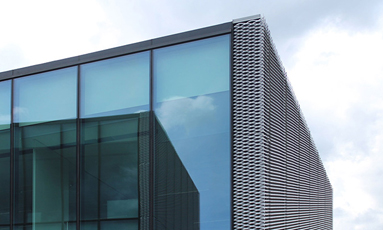
A first-hand experience attests to the multifaceted nature of thin metal sheets with holes. Using these sheets, manufacturers can address issues such as ventilation, filtration, and even aesthetics. For instance, in the architecture field, perforated sheets become an artistic component. When integrated into buildings, they provide not only aesthetic appeal but also practical benefits like shade and airflow management, which enhance energy efficiency.
Delving into the expertise of producing these sheets involves understanding the materials compatible with the intended application. Manufacturers will choose specific metals based on properties such as strength, weight, durability, and resistance to corrosion. Stainless steel offers excellent resistance to rust and corrosion, making it ideal for outdoor and weather-exposed applications. On the other hand, aluminum is lightweight yet robust, beneficial for applications where reduced weight is crucial.
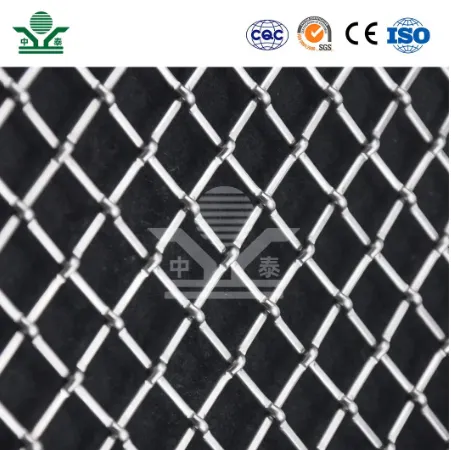
The authoritativeness of perforated metal sheets is clear when considering their use in industries such as automotive, aerospace, and food processing, where precision and quality cannot be compromised. For example, in the automotive industry, these sheets are employed in the manufacturing of grilles and vents, which must withstand environmental stressors, yet provide options for designers to incorporate style elements seamlessly. In aerospace, the weight of every component matters, and perforated metal sheets offer a perfect balance between structural integrity and weight reduction.
thin metal sheet with holes
Trustworthiness in the use of these sheets is established through rigorous testing and quality assurance processes. Manufacturers rely on industry standards and certifications to produce sheets that meet or exceed regulatory requirements. Clients and end-users look for certified products, knowing they promise enhanced performance and safety.
Thus, selecting thin metal sheets with holes involves considering factors such as the size and pattern of perforations. Precise perforation patterns are not only crucial for aesthetic reasons but also influence the performance of the product in its application. Accurate perforation ensures optimal airflow and sound diffusion, which is vital in applications like acoustic panels.
For those who may be new to working with perforated metal sheets, connecting with seasoned professionals can provide insights into the most effective use of these materials. Collaboration with engineers and designers can maximize the potential benefits of the sheets, ensuring that the final product is both functional and aligns with the intended design vision.
In conclusion, thin metal sheets with holes are more than simple components; they represent a convergence of design, functionality, and innovation. With strategic use across various sectors and a careful selection process aligning with professional standards and certifications, these sheets can provide enhanced performance and aesthetic value. Whether employed in high-tech industries or creative architectural designs, their role in advancing efficiency and design is undeniable. Making informed decisions about the selection and application of perforated metal sheets stems from a blend of personal expertise, industry knowledge, and the pursuit of excellence.