Navigating the world of construction materials comes with contemplating various factors, notably cost effectiveness and suitability to the specific needs of a project. Steel grating is an integral component in an array of infrastructure applications due to its strength, durability, and versatility. Perfectly suited for industrial flooring, walkways, platforms, and safety barriers among others, steel grating is a preferred choice in environments requiring high load-bearing capacity.
The focus often turns to its cost per square foot, a crucial point in budgeting for projects.
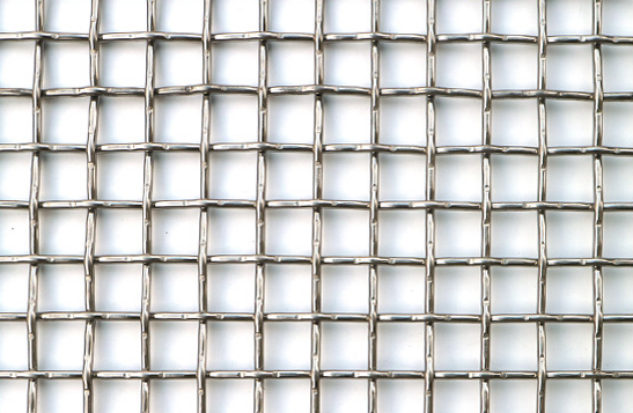
Accurately assessing the cost per square foot of steel grating involves understanding several dynamic elements. Primarily, the type of steel employed significantly influences the price. Typically, carbon steel is cast as a go-to option for its affordability and robustness. Alternatively, stainless steel, though commanding a higher price point due to its exceptional resilience against corrosion and rust, is ideal for environments with extreme exposure to moisture and chemicals.
The design and manufacturing process further dictate cost considerations. Grating can be divided into several categories, with bar grating being the most common. It’s composed of parallel bars joined by cross bars to form a grid. Within this category lies several subtypes welded, press-locked, and swage-locked gratings. Welded bar grating, known for its superior strength and simplicity in manufacturing, tends to cost less compared to press-locked or swage-locked variations, which offer additional aesthetic or environmental benefits.
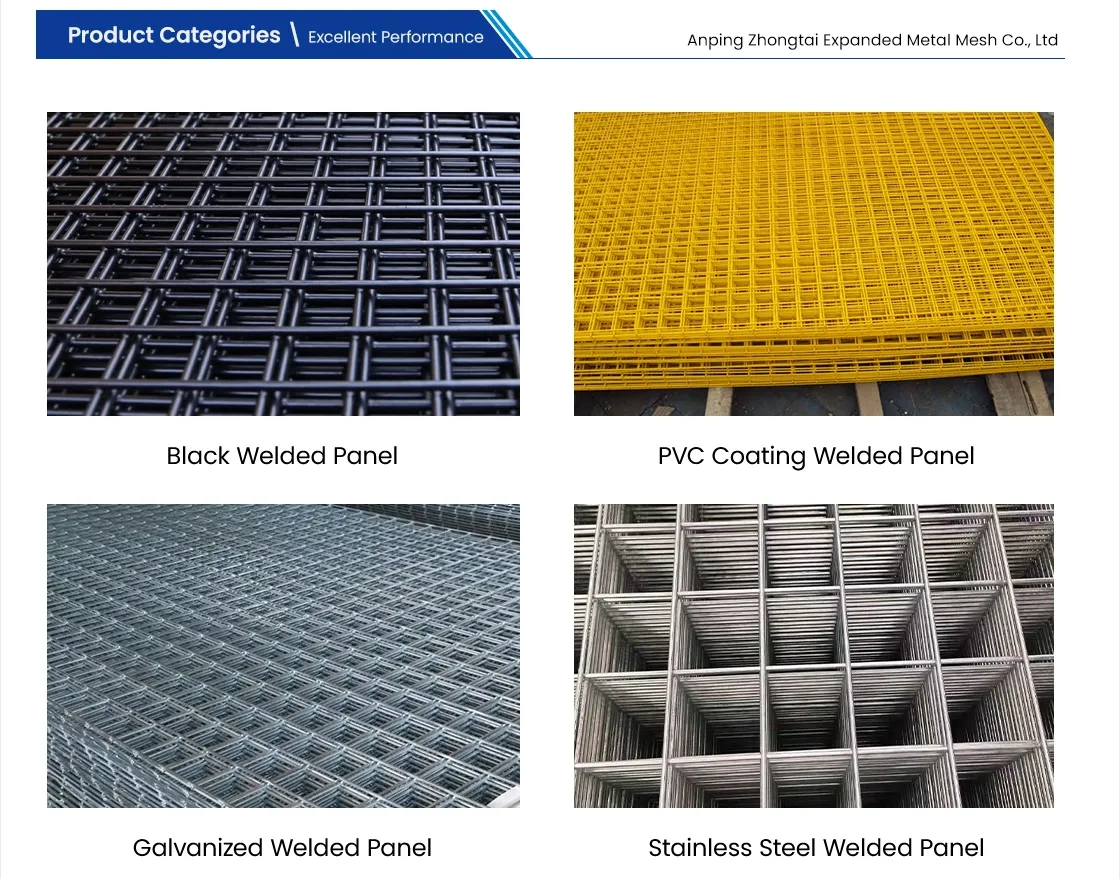
Dimensions and thickness also play a pivotal role in cost calculation. Grating thickness typically ranges from 1 inch to 3 inches, and the thicker the grating, the higher the cost due to increased material usage. Similarly, the bar spacing – standard, close, or custom – impacts the finish cost. Increased bar density correlates to heightened safety and load-bearing attributes at an additional expense.
The strategic coating applied to steel grating significantly impacts its longevity and maintenance costs. Galvanization, the process of applying a protective zinc coating to prevent corrosion, hikes the initial cost but can prolong the grating's lifespan manifold. For environments where aesthetics are pivotal, or there is a unique architectural requirement, powder coating offers an appealing alternative, attracting higher costs but delivering premium finishes.
steel grating cost per square foot
Geographic factors, including local availability of raw materials, logistics, and regional labor costs, must be contemplated. Procuring steel grates from local suppliers may reduce transportation costs and influence the price point per square foot due to reduced overheads.
Installation is another crucial dimension in determining the overall expenditure associated with steel grating. While simple installations could be conducted internally, complex arrangements may necessitate professional intervention, further escalating costs. Additionally, maintenance expenses over the product's lifecycle, though often overlooked in initial estimations, can reflect heavily on long-term financial planning. Regular upkeep is necessary to prevent damage or degradation, especially in harsher environments.
In practical terms, expecting a broad range for the cost per square foot – from $15 to $50 or more – isn’t atypical. This variance underscores the necessity of detailed market research and thorough project requirement analysis. Project planners and procurement officers should leverage comprehensive quotes and engage reputable suppliers to ensure investment in quality and cost-effectiveness.
The ongoing innovation in manufacturing processes and increased emphasis on sustainability also suggests potential shifts in future pricing metrics. As such, understanding the production and supply chain dynamics allows key stakeholders to forecast and budget more accurately, reflecting the increasingly multifaceted nature of the global construction landscape.
Ultimately, the prudent integration of cost considerations with material performance and project specifications empowers stakeholders to make informed decisions, optimizing both financial and functional outcomes in the curated use of steel grating solutions.