Perforated sheets have become an integral component across various industries due to their versatility, functionality, and aesthetic appeal. However, understanding the cost factors involved is crucial for businesses looking to incorporate these materials effectively. Here, we dissect the elements that influence the cost of perforated sheets, ensuring you are well-equipped to make informed purchasing decisions.
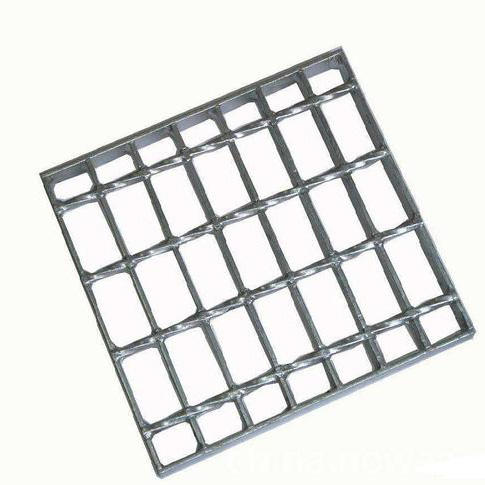
Perforated sheets, typically made from metals such as aluminum, stainless steel, or carbon steel, are engineered to feature holes, slots, or decorative patterns. The manufacturing process, raw materials, and specific design requirements can significantly influence the overall cost. From construction to interior design, automotive to agricultural applications, the requirement for tailored solutions often dictates the expenditure.
Firstly, the type of material selected is a primary cost determinant. Stainless steel, known for its durability and corrosion resistance, generally incurs a higher cost compared to other metals like aluminum or mild steel. Aluminum sheets offer a lightweight alternative with reasonable strength and resistance to oxidation, making them suitable for applications requiring light loads. The choice of material should align with environmental conditions and performance expectations, which requires expert consideration of material properties.
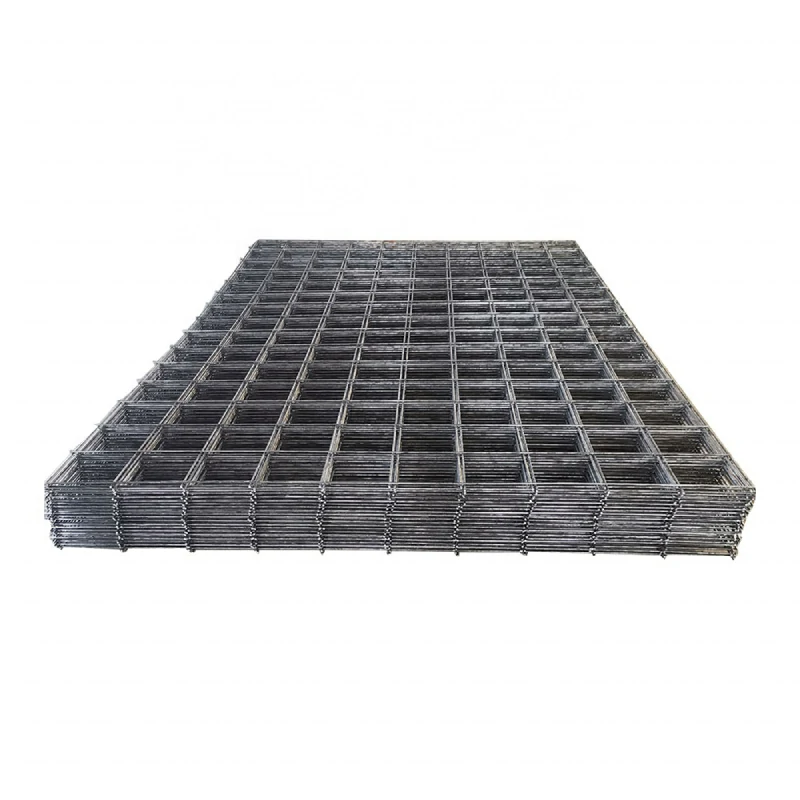
The complexity of the perforation pattern is another critical aspect. Simple, uniform perforated patterns are more cost-effective due to reduced manufacturing time and less wear on machinery. Conversely, intricate designs that involve precise hole sizes, unusual shapes, or specific arrangements often necessitate advanced technology, such as CNC machinery, to achieve the desired finish. This not only increases production time but also necessitates skilled labor, subsequently raising costs.
perforated sheet cost
Volume and order size also play a pivotal role in pricing. Bulk purchases typically offer economies of scale, reducing the cost per unit. However, for custom-designed sheets with specific perforation patterns, smaller orders might attract higher costs due to the initial setup and low production efficiency. It’s essential to balance the need for customized solutions with cost-effective practices by consulting with manufacturers to optimize order quantities.
Surface treatment and finishing processes also affect pricing. Techniques such as galvanizing, powder coating, or anodizing provide additional protection and aesthetic enhancement, extending the sheet's lifespan and performance. Each process comes with its distinct cost implications and benefits, thus requiring a comprehensive analysis of the intended application environment and desired longevity. Professional consultation with material engineers or specialists can ensure that the chosen finish aligns with both functional needs and cost constraints.
Transportation and handling costs should not be overlooked. The weight and bulkiness of perforated sheets can impact shipping costs significantly, especially for long-distance or international deliveries. Selecting local suppliers where possible can not only minimize these costs but also offer quicker turnaround times and reduced environmental impact.
In conclusion, while perforated sheets offer numerous benefits, a detailed understanding of the factors influencing their cost is imperative. From material selection and perforation complexity to volume considerations and finishing details, each component requires careful evaluation. By aligning these factors with project requirements and budget, businesses can ensure they acquire high-quality perforated sheets that deliver maximum value. Consulting industry experts remains indispensable, providing insights into the latest trends and technologies that can further optimize both performance and expenditure. Such expertise not only enhances decision-making but also fortifies trust, ensuring reliability and satisfaction in every perforated sheet investment.