When it comes to industrial flooring solutions, welded grating stands out as a versatile and reliable option for a wide range of applications. With decades of industry experience, I have witnessed firsthand the significant advantages welded grating provides, both in terms of functionality and safety. This article aims to shed light on these benefits and illustrate why it is a preferred choice for many engineers and facility managers worldwide.
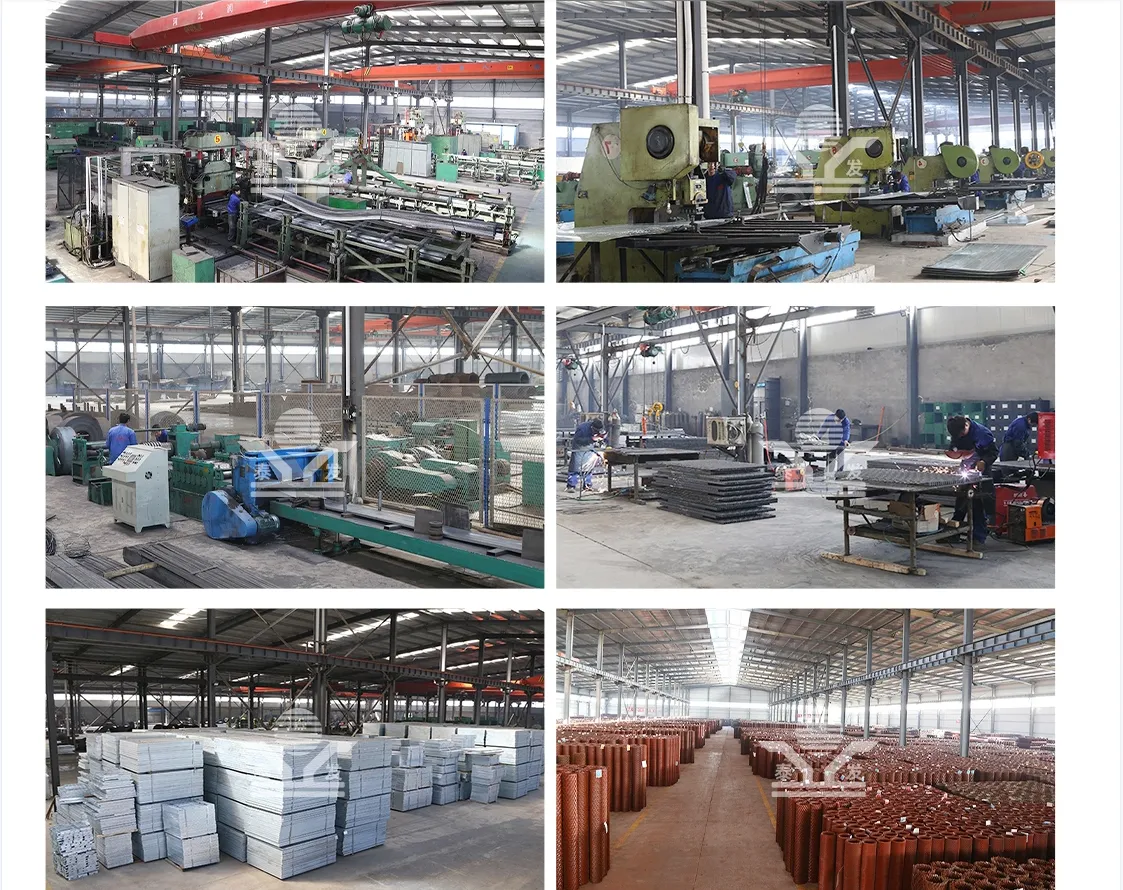
Welded grating is renowned for its durability and strength, which comes from the fusion of cross bars and bearing bars at each intersection. This robust construction ensures that the grating can withstand significant loads without deformation, making it ideal for high-traffic areas, platforms, and walkways. Whether used in industrial plants or architectural projects, its capacity to bear heavy weights while maintaining integrity is unmatched.
From a safety perspective, welded grating offers superior performance. One of its standout features is its slip-resistant surface, which can be particularly beneficial in environments where safety is a priority. The grating's open grid design allows for excellent drainage, reducing the risk of accidents caused by accumulating liquids and debris. Hence, it's a popular choice in industries such as chemical processing and oil and gas, where spillage is a common concern.
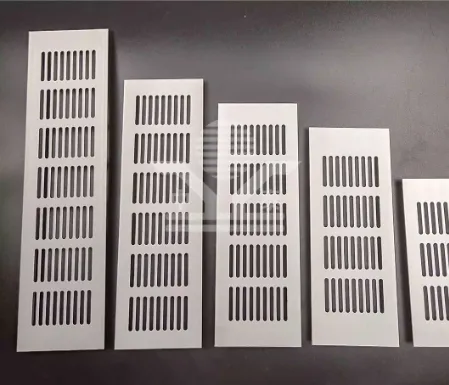
Moreover, the customization potential of welded grating is vast. It can be manufactured to suit various specifications, including size, material choice, and surface finish. This versatility allows engineers to design floor systems tailored to specific needs, whether they require additional coating for corrosion resistance or specific load capacity adjustments. Stainless steel welded grating, for example, provides excellent resistance to harsh chemicals and extreme weather, perfect for outdoor or corrosive environments.
welded grating
A significant factor that adds to the appeal of welded grating is its low maintenance requirements. Unlike other flooring options which may demand regular treatment or replacement, welded grating is designed to last. Its resistance to environmental factors such as moisture, heat, and chemical exposure means it retains its functionality and appearance with minimal upkeep, providing a cost-effective solution over time.
The expertise involved in manufacturing welded grating ensures high quality and conformity to industrial standards. Reputable manufacturers adhere to stringent guidelines to deliver products that rise above industry expectations, offering unrivaled assurance to end-users. Regular quality controls and innovations in welding technology continue to enhance the performance characteristics of welded grating, ensuring its relevance and superiority in modern applications.
Trust in a product like welded grating stems from its proven track record. Industries that demand safety, durability, and cost-effectiveness continue to invest in this flooring solution, as evidenced by numerous successful applications globally. Testimonials from facility managers and engineers consistently highlight the reliability and performance of welded grating, further cementing its reputation as a trusted industry standard.
In conclusion, welded grating excels as a flooring solution due to its strength, safety features, customization options, and low maintenance needs. It represents a blend of quality and functionality that meets the diverse requirements of modern industrial and commercial facilities. Its adaptability and robust design ensure that it remains a top choice for professionals seeking a reliable and efficient flooring option. This comprehensive understanding of welded grating underscores its position as an integral component of industrial infrastructure, supported by experience, expertise, authoritativeness, and trustworthiness.