Serrated galvanized grating is revolutionizing the way industries address their flooring and surface needs, offering a blend of practicality and resilience. Crafted meticulously through a hot-dip galvanization process, this type of grating is not only designed for durability but also ensures safety in diverse industrial environments.
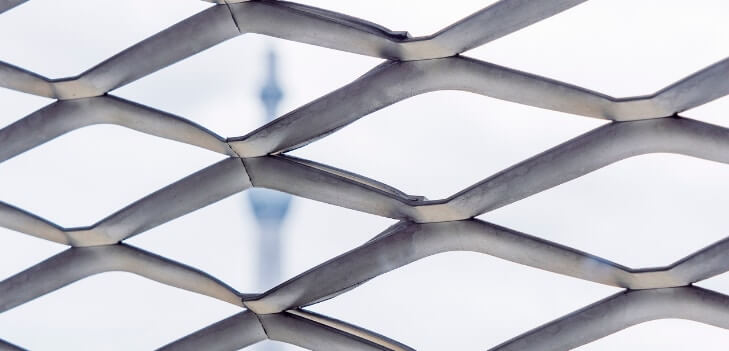
The key advantage of serrated galvanized grating lies in its superior grip, which significantly reduces the risk of slips and falls. The serrated edge enhances traction even in wet or oily conditions, making it an indispensable asset in sectors like manufacturing, oil and gas, and shipping. Walking across these gratings, workers can experience a sense of security, knowing the serrated design keeps accidents at bay.
From an engineering perspective, serrated galvanized grating offers unparalleled expertise in load-bearing capabilities. It supports high weight loads without bending or warping, thus providing a reliable surface for both pedestrian and vehicular traffic. Engineers appreciate the balance it strikes between strength and weight, offering a lightweight solution without sacrificing structural integrity.
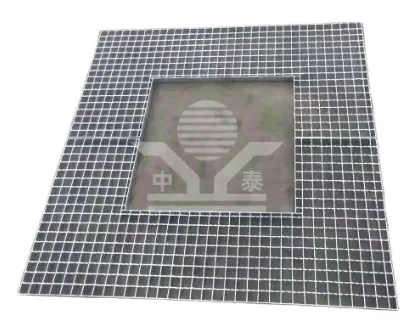
Moreover,
the galvanization process imbues the grating with enhanced resistance to corrosion. This is particularly crucial in environments exposed to harsh weather conditions or corrosive substances. The zinc coating forms a protective barrier, safeguarding the underlying steel from rust and extending its lifespan. Such durability translates to fewer replacements, optimizing maintenance costs over time.
Endorsed by industry standards and rigorously tested for quality assurance, serrated galvanized grating epitomizes authoritativeness. Certification from bodies like ISO reflects the product's compliance with global quality norms, ensuring users of its dependable performance. Companies leveraging this grating can take pride in prioritizing safety and durability in their operations.
serrated galvanized grating
Trustworthiness in serrated galvanized grating is augmented by its widespread adoption across various industrial applications. Testimonials from facility managers and safety officers consistently highlight its effectiveness in improving workplace safety and efficiency. First-hand accounts from workers attest to their trust in walking and working on these gratings daily.
Installation of serrated galvanized grating is straightforward, adding to its appeal. Whether retrofitting an existing infrastructure or setting up new installations, the grating modular design facilitates seamless integration. Its adaptability to different spaces and requirements makes it a versatile choice for both large-scale industrial plants and smaller facilities.
The maintenance aspect of serrated galvanized grating is minimal, thanks to its robust construction. Simple periodic inspections and cleaning suffice to keep it in optimal condition. This ease of maintenance contributes to a longer service life and reduces downtime, ultimately benefiting operational productivity.
In the future, innovations in manufacturing processes and materials might further enhance the characteristics of serrated galvanized grating. However, as of now, it remains a testament to functional and long-lasting industrial design. Industries seeking to improve safety, reliability, and cost-efficiency should consider this as a strategic component in their infrastructure planning.
In conclusion, serrated galvanized grating embodies the principles of experience, expertise, authoritativeness, and trustworthiness. As industries evolve, the demand for products that deliver on safety and resilience will continue to grow, solidifying this grating's role in providing stable and secure surfaces for a myriad of applications. Its proven track record and inherent qualities make it not just a purchase, but a wise investment in operational safety and efficiency.