In the nuanced realm of industrial flooring solutions, platform grating emerges as a pivotal element, often defined by its impressive functional adaptability and structural durability. Businesses pivoting towards sophisticated infrastructure identify platform grating not just as a flooring option, but as a cornerstone of operational efficiency and safety. The weight of platform grating is a critical factor that meticulously influences its selection and application across various sectors, reflecting nuances of engineering professionalism and practical reliability.
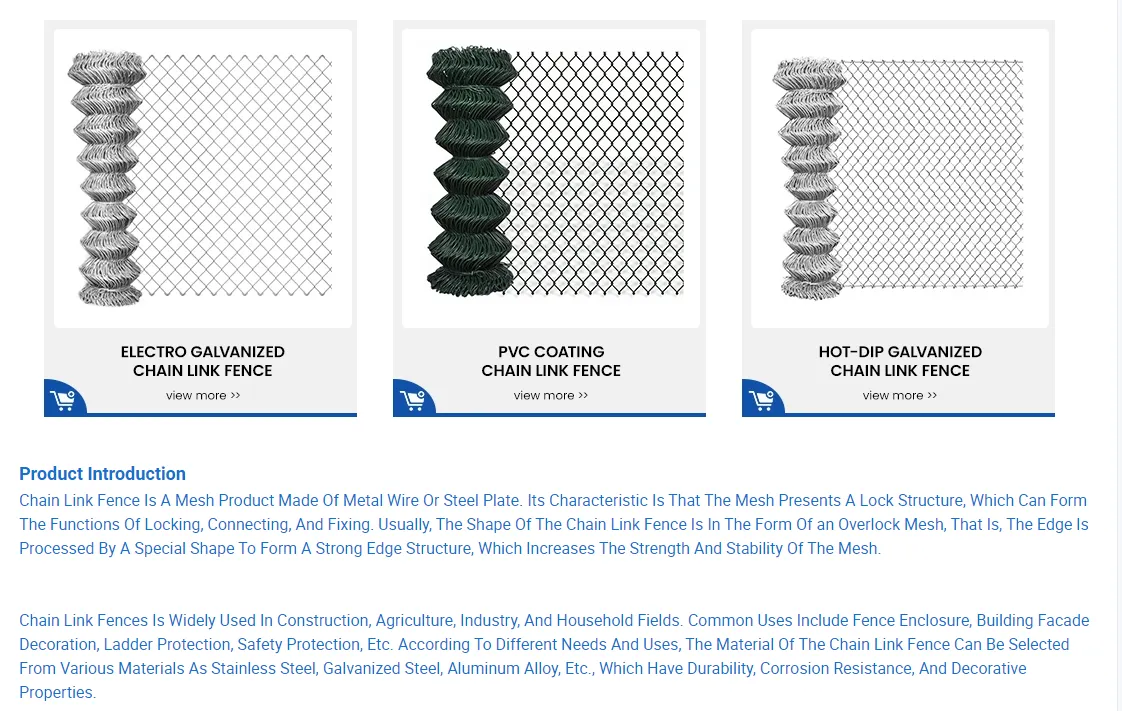
Firstly, understanding the weight of platform grating is crucial as it directly correlates with load-bearing capabilities and installation feasibility. The weight is intrinsically linked to the material composition and design specifications—important for engineers and procurement specialists who prioritize safety and compliance. Common materials include steel, aluminum, and fiberglass, each bringing distinct weight attributes and strengths. Steel is renowned for its robustness and substantial weight, fitting scenarios demanding maximum strength. Conversely, aluminum offers a lighter, corrosion-resistant alternative, suitable for environments where weight reduction is paramount while maintaining sufficient strength.
Moreover, the grating's design intricacies, such as bearing bar size and spacing, also play a crucial role in its overall weight. Architects and industry experts often opt for customized grating systems, tailoring these parameters to meet specific load requirements and spatial constraints. For instance, a denser bar pattern will increase weight, thereby enhancing load capacity—a vital consideration in heavy industrial settings where safety margins are non-negotiable.
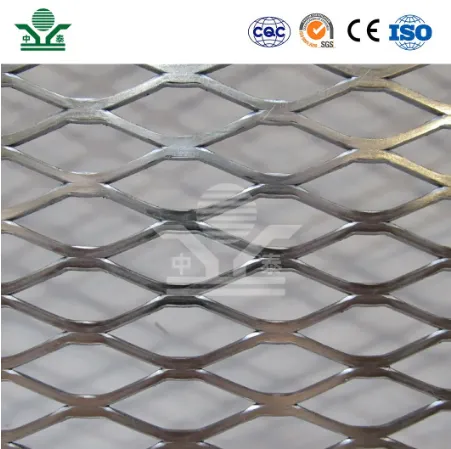
Another professional consideration is the impact of platform grating weight on installation logistics and operational upkeep. Heavier grating, while robust, demands more in terms of handling and installation equipment, potentially escalating operational costs. Thus, facilities with budget constraints or those aiming for swift installation processes might opt for lighter alternatives like fiberglass grating. Fiberglass is particularly valued for its non-conductivity and lighter weight, making it easier and more cost-effective to handle without compromising on safety attributes.
Furthermore, the weight factor inherently affects transportation logistics—a significant concern for procurement departments. A heavier load incurs higher shipping costs and may necessitate specialized transport arrangements, impacting the final installation budget. On the other hand, lighter materials reduce these costs and allow for more straightforward, less resource-intensive logistics. Hence, a thorough cost-benefit analysis addressing both short-term and long-term projections is indispensable for decision-makers responsible for infrastructure investment.
platform grating weight
The expertise of engineers and builders comes to the fore when distinguishing between practical and theoretical weight specs during installation processes.
Authentic real-world application and testing often uncover insights beyond basic catalog specifications. Stakeholders with experience in resilient infrastructure systems emphasize prototypes and testing in actual operating conditions to ensure that the platform grating weight aligns seamlessly with real-world performance expectations.
From an authoritativeness perspective, utilizing data-backed insights and adhering to industry standards resonate profoundly across all engineering and procurement narratives. Professionals frequently reference standards such as the ASTM specifications for load capacity and material quality, enriching decision-making processes with a layer of undeniable credibility. Companies that prioritize such authoritative references not only guarantee compliance but also elevate their operational trustworthiness, reassuring stakeholders that their infrastructure investment is well-founded.
Establishing trust involves more than adhering to technical specifications—it’s about conformity with industry best practices and transparency in communication concerning maintenance protocols and lifespan expectations. Quality platform grating suppliers provide comprehensive warranties and post-sales support, fortifying the trust of their industrial patrons. This assurance becomes particularly significant when considering potential repair or replacement scenarios—well-built, correctly weighted grating mitigates these risks, offering long-term operational stability.
In sum, platform grating weight is far from a trivial specification—it’s a multifaceted determinant bridging engineering precision, operational pragmatism, and strategic foresight. For firms and industries navigating the complexities of modern infrastructure, an astute understanding of this critical attribute supports informed decisions, ensuring safety, efficiency, and sustainability in their engineering endeavors. The seamless integration of such expert insights into grating selection reinforces not just the physical structures in industries, but also fortifies the foundational knowledge essential to progress and innovation in the field.