Perforated sheet metal, particularly in the standard size of 4 x 8 feet, is an indispensable material across numerous industries due to its versatility and adaptability. Professionals working with this material appreciate its myriad benefits, which stem from a combination of high-quality manufacturing and versatile application.
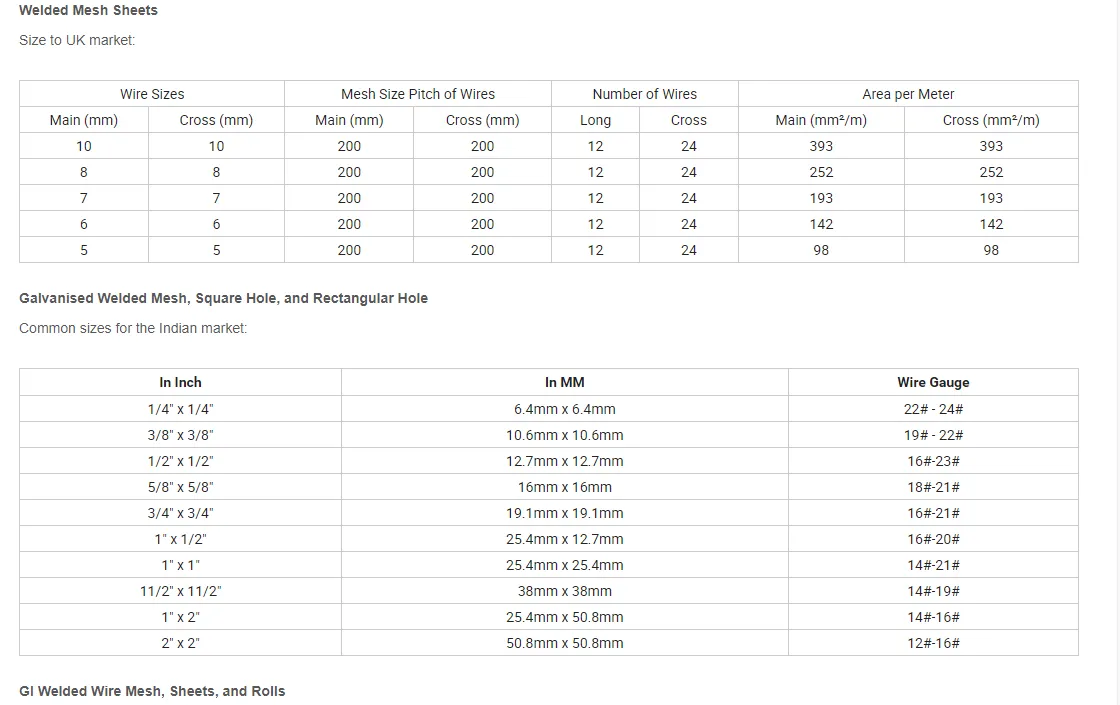
For engineers and designers, the 4 x 8 perforated sheet metal offers a practical solution for an array of structural and aesthetic needs. The process of perforating metal sheets typically involves punching or pressing to create patterns of holes or slots, transforming plain sheets into dynamic, multifunctional components. The 4 x 8 size is particularly favored due to its convenience; it is large enough for significant coverage yet manageable for fabrication processes.
From an engineering perspective, one of the critical attributes of perforated sheet metal is its lightweight nature without compromising structural integrity. This characteristic is crucial in sectors like automotive manufacturing, where reducing weight is essential for improving fuel efficiency. The evenly distributed perforations reduce the overall weight of the metal sheet while still maintaining the strength and rigidity required for structural applications.
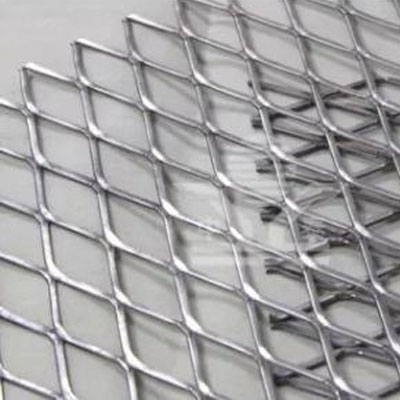
In architectural design, the adaptability of 4 x 8 perforated sheet metal enables creative solutions for both functional and decorative applications. When used in building facades, screens, or interior partitions, it allows for airflow and light diffusion while providing privacy and a modern aesthetic. Different materials, such as aluminum, stainless steel, and brass, offer unique properties—aluminum for its corrosion resistance, stainless steel for its durability, and brass for its decorative appeal—allowing architects to choose based on project-specific needs.
Expertise in handling and working with perforated sheet metal also implies understanding the impact of different perforation patterns and spacing on the performance of the material. For instance, when used in acoustics, perforated sheets can significantly enhance sound absorption, making them ideal for environments where noise reduction is paramount, such as concert halls and auditoriums. This application requires careful consideration of hole size, pattern, and spacing, all of which influence acoustic properties.
perforated sheet metal 4 x8
From a product customization angle, manufacturers offer a wide range of hole patterns—round, square, slotted—and can even create bespoke designs tailored to specific client needs. This capability not only broadens the application scope but also allows brands to add unique identifiers to their projects, enhancing their distinctiveness and aesthetic appeal.
Trust in perforated sheet metal products is often reinforced by the adherence to stringent quality standards and certifications. Reliable suppliers ensure that their 4 x 8 sheets meet industry benchmarks, offering assurance to customers regarding the material's performance and durability. This trust is crucial in industries where safety and reliability are non-negotiable, such as aerospace and construction.
The use of perforated sheet metal in filtration demonstrates its authoritative role in scientific and industrial processes. Its application in filtration systems is vital for air and liquid separation, providing efficiency and effectiveness in separating particles due to the precise nature of the perforations. These systems are pivotal in industries ranging from food processing to petrochemicals, underscoring the material's multifunctionality.
Overall, the practical applications of 4 x 8 perforated sheet metal, combined with its customizable nature, render it an asset across various domains. Professionals seeking materials that offer both functionality and aesthetic versatility will find perforated sheet metal an invaluable component in their toolkit. Its widespread use and established reliability speak to its authority and trust in the marketplace, making it a staple choice for those who demand quality and performance.