Perforated metal plates have been around for decades, serving a myriad of purposes in industries ranging from architecture to automotive. These versatile components have evolved from simple sheets of metal with holes to sophisticated products that balance form and function, offering both aesthetic appeal and practical benefits.
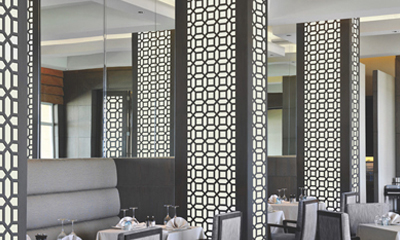
In my extensive experience as a materials engineer specializing in metal applications, I have witnessed firsthand the transformative impact these plates have across various domains. Perforated metal plates are primarily recognized for their unique ability to integrate seamlessly into both structural and decorative roles in a project. Their inherent strength, coupled with lightweight properties, makes them incredibly adaptable to different engineering and architectural requirements.
One of the most significant advantages of perforated metal plates is their ability to provide excellent air and light dispersion while maintaining a degree of privacy and protection. For instance, in building facades, these plates serve as a superior alternative to traditional materials, allowing natural airflow and light entry while preserving core privacy — a feature particularly beneficial in urban developments where space is at a premium.

Furthermore, from a technical perspective, these plates contribute to sound attenuation, proving invaluable in environments where noise reduction is paramount. Industries such as construction and manufacturing utilize perforated metal plates to minimize noise impact from machinery, thus enhancing workplace safety and reducing environmental noise pollution.
The specialization of these plates extends into bespoke design capabilities. Modern advancements in manufacturing technology have enabled custom perforation patterns that cater to specific functional needs and creative visions. From custom geometric designs to intricate, art-like patterns, the possibilities are boundless, effectively allowing architects and designers to push the boundaries of conventional aesthetics.
perforated metal plate
When assessing the expertise embedded in producing high-quality perforated metal plates, it is essential to appreciate the precision involved in their manufacturing. Utilizing advanced techniques such as laser cutting, CNC machining, and automated punching, manufacturers can achieve exacting standards that meet stringent industrial regulations. This precision not only guarantees dimensional accuracy but also ensures consistency in performance across different applications.
Authoritativeness in choosing perforated metal plates comes from associating with reputable manufacturers who uphold rigorous quality control standards. Ensuring that the plates are crafted from premium materials, whether aluminum, stainless steel, or otherwise, guarantees longevity and durability, crucial factors in long-term infrastructural projects. Furthermore, partnering with certified suppliers offers peace of mind that the products will meet or exceed expected standards, adding an additional layer of trustworthiness.
Beyond the product itself, sustainability has become a key consideration in the selection of materials.
Perforated metal plates are typically produced from recyclable metals, aligning with global efforts towards sustainable development. Their use helps reduce a project's carbon footprint by enhancing energy efficiency through passive cooling and reduced lighting needs, showcasing their role in eco-friendly building solutions.
My encounter with the multifaceted applications of perforated metal plates has underscored their importance as a critical component in modern design and engineering domains. Beyond their technical benefits, they appeal to a growing demand for sustainable, functional, and aesthetically pleasing construction methods. As the marketplace continues to evolve, the role of perforated metal plates is set only to expand, driven by innovations in material science and architectural design. This evolution posits exciting opportunities for industries looking to innovate and push forward with solutions that harmonize functionality with creativity.
In conclusion, perforated metal plates are not only a testament to engineering ingenuity but also a pivotal element in the ongoing narrative of sustainable and adaptive design strategies. Engaging with these products means investing in quality, experience, and forward-thinking—a decision that aligns with both immediate project needs and long-term environmental goals.