Perforated copper foil, a niche yet incredibly versatile material, is rapidly gaining traction across numerous industries, heralding a new era of innovation and efficiency. While the layman might overlook the potential of this seemingly simplistic material, insiders recognize its multifaceted applications that spur advancements in technology and design.
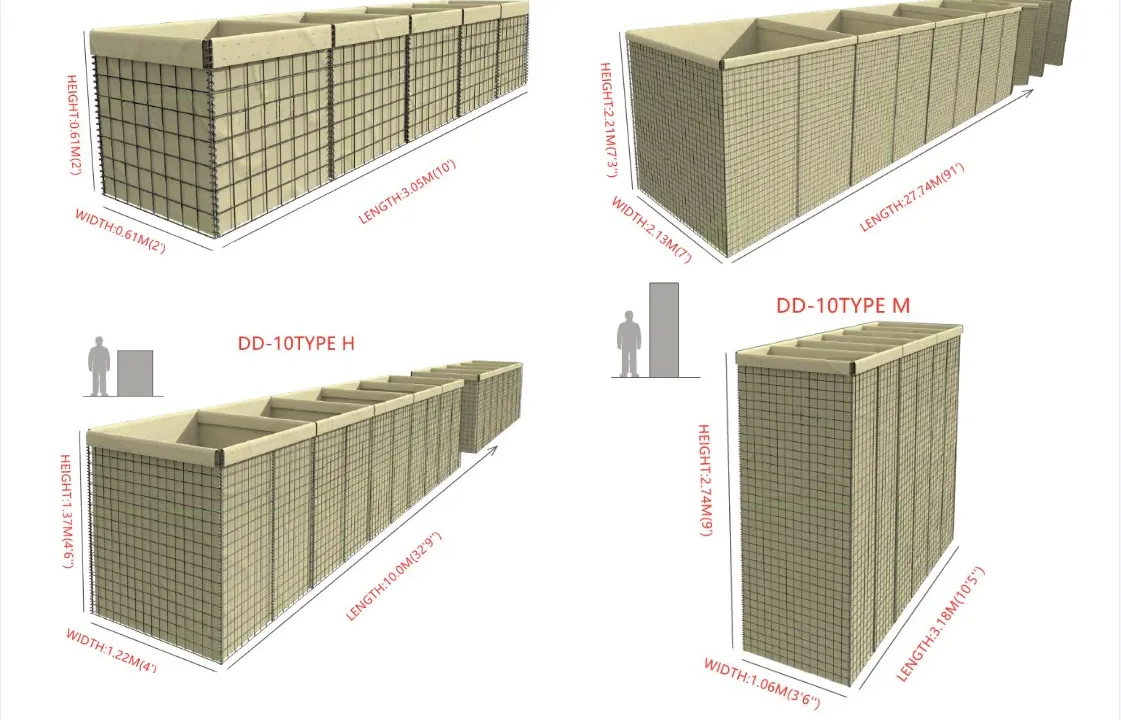
From the lens of experience, those who have worked extensively with perforated copper foil testify to its unparalleled utility in heat dissipation and electromagnetic interference (EMI) shielding. The intricate perforations significantly augment the foil's surface area, thereby enhancing its heat-dissipating capabilities. This feature is especially valuable in the electronics industry, where maintaining optimal temperatures is crucial for device longevity and performance. Engineers and designers often share anecdotes of components running cooler and more efficiently, attributing it to the strategic inclusion of perforated copper foil.
Delving into the expertise domain, it's pertinent to highlight the manufacturing precision involved in producing perforated copper foil. This material requires high-grade copper that ensures excellent conductivity and minimal signal loss, making it indispensable in high-frequency applications. Precision in perforation patterns also plays a critical role; varying the size, shape, and distribution of holes can tailor the material's properties to specific needs. Whether it's enhancing acoustic performance in audio equipment or optimizing airflow in cooling systems, the meticulous engineering behind perforated copper foil aligns perfectly with the demands of cutting-edge applications.

Authoritativeness in the realm of perforated copper foil is underscored by its adoption by leading innovators in technology sectors. Companies pioneering advancements in renewable energy, for instance, employ perforated copper foil in solar cells to augment conductivity while reducing weight. Similarly, aerospace engineers utilize this material to create lightweight, conductive surfaces for various components. The credibility of these applications is enhanced by rigorous industrial standards and certifications that guarantee performance under the most stringent conditions.
perforated copper foil
The trustworthiness of perforated copper foil is further solidified by longstanding partnerships between suppliers and manufacturers who adhere to environmentally and ethically responsible production methods. As sustainability becomes a cornerstone in material selection,
copper's recyclability stands out. The perforation process, optimized to minimize waste, complements copper's natural propensity for reuse, resonating well with eco-conscious design philosophies.
Looking at product innovations, recent developments highlight the scalability and adaptability of perforated copper foil. The rise of 5G technology necessitates components that deliver high conductivity and effective EMI shielding, both achievable with this material. Additionally, the automotive industry, with its shift towards electric vehicles, is exploring perforated copper foil as a light yet efficient conductor to manage heat in battery systems and electronic modules.
This material's growing repertoire of applications cements its status as a staple in modern engineering and manufacturing. From startups to established conglomerates, the pivot towards more sustainable and efficient materials has shone a spotlight on perforated copper foil, making it a sought-after choice for innovative solutions.
In conclusion, perforated copper foil represents a confluence of experience, expertise, authoritativeness, and trustworthiness. Its multifaceted advantages extend far beyond basic conductive functionality, offering unique solutions across industries. Those who grasp its full potential are poised to lead in domains that prioritize efficiency, sustainability, and groundbreaking design. As global industries strive to optimize and innovate, perforated copper foil will undoubtedly remain at the forefront, a testament to the power of refined material science and engineering.