Forge welded grating, a prominent industrial component, is renowned for its robustness and versatility. Industries worldwide are gravitating towards this grating solution due to its proven durability and high load-bearing capacity, necessities that meet a multitude of sector-specific demands.
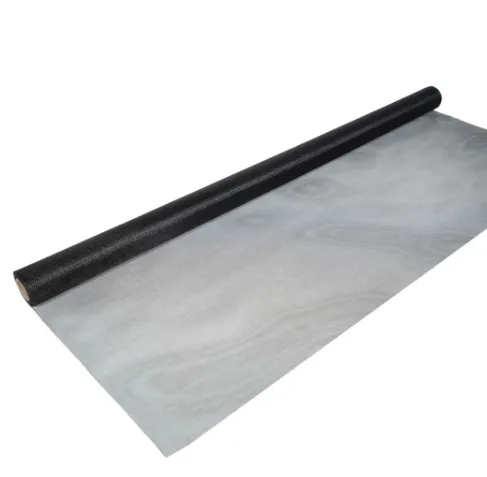
Experiencing forge welded grating firsthand reveals its unmatched strength and adaptability across different applications. Notably utilized in sectors like manufacturing, petrochemical, and even architectural design, forge welded grating is crafted from a meticulous process. This involves joining cross bars to bearing bars by applications of intense heat and pressure. The result is a permanent, sturdy intersection that offers enhanced strength compared to traditional grating systems. This method produces a grating that retains structural integrity under strenuous conditions, a critical consideration for industries requiring rigorous performance standards.
In terms of expertise, understanding the forging process sets this grating apart. Forge welding relies on the principle of coalescence, a metal-joining technique that facilitates robust bonding without additional materials like adhesives. Mastery over this technique ensures reduced chances of slippage, making it a safer choice for flooring, walkways, and platforms. Additionally, expertise in selecting the right materials for welding—typically stainless steel or carbon steel—impacts the grating's resistance to corrosion and its capability to function in hostile environments.
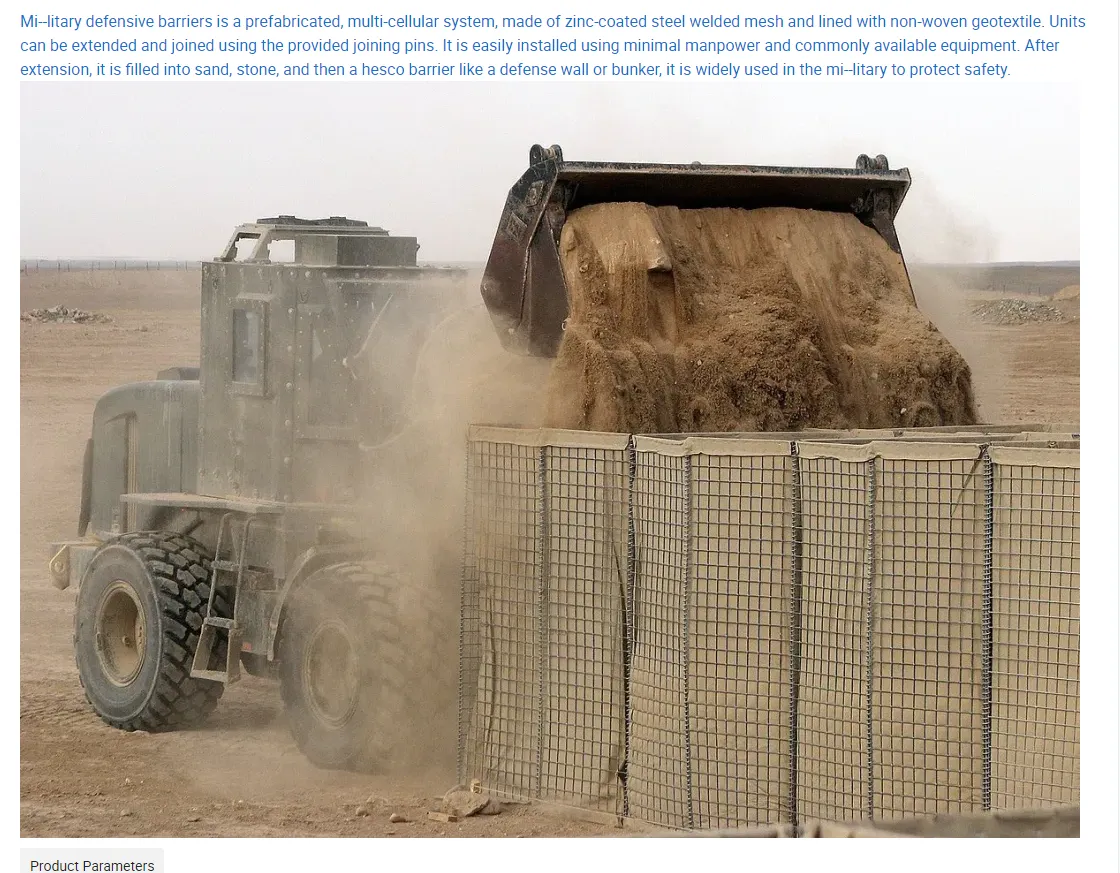
Authoritativeness is established through the credentials of manufacturers and their adherence to international standards. Trustworthy manufacturers demonstrate compliance with safety norms and engage in rigorous testing procedures to validate their products. Often, they hold certifications from bodies such as the American Welding Society (AWS) or similar regulatory authorities, which attests to the reliability and quality of their forgings. This credibility is an assurance to consumers and industrial partners, instilling confidence in the product's efficacy.
forge welded grating
Trustworthiness in forge welded grating is not only derived from material quality but also from the experiences shared by seasoned professionals in the field. Testimonials from engineers and project managers who have implemented these gratings highlight significant reductions in maintenance costs and improved safety outcomes. This user feedback is invaluable, offering insights into real-world applications where these gratings have consistently exceeded expectations.
From a products perspective, customization is a key advantage of forge welded grating, allowing adjustments to be made for specific load requirements or environmental conditions. Clients can specify dimensions, materials, and finishes, tailoring the product to their precise needs. This customizability ensures that projects, whether involving small mezzanine installations or extensive industrial platforms, benefit from a bespoke solution that precisely fits their operational parameters.
Moreover, sustainability is an emerging consideration that cannot be overlooked. Forge welded gratings are often made from recyclable materials, aligning with global efforts to reduce industrial waste. The longevity of these gratings further contributes to environmental preservation; their prolonged lifecycle means fewer replacements and a smaller carbon footprint over time.
In conclusion, forge welded grating stands out due to its exceptional strength, versatility, and reliability. By choosing this option, industries not only invest in a superior product but also gain the assurance of safety, sustainability, and tailored solutions adapted to their unique requirements. As the global industrial landscape continues to evolve, the demand for high-performance grating solutions like forge welded grating is expected to grow, driven by their capacity to meet and exceed the stringent demands of modern applications.