Navigating the intricacies of bar grating cost can often feel daunting, especially when seeking a product that marries durability with affordability. Having spent over a decade in materials procurement for various industrial applications, this article draws upon extensive experience and industry expertise to provide a comprehensive view of bar grating costs, helping you make informed purchasing decisions.
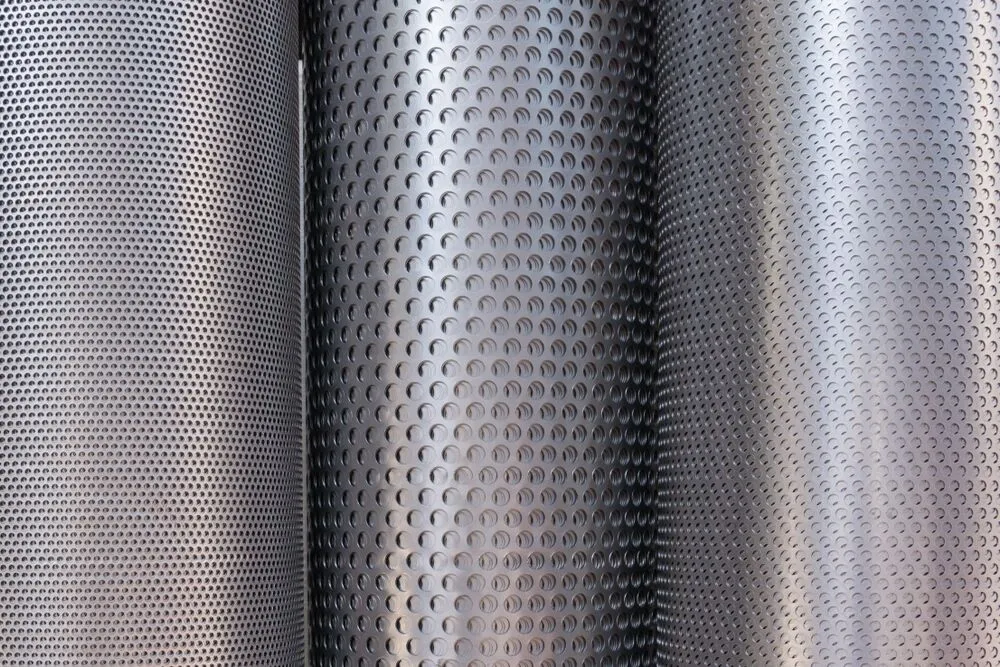
Bar grating, a versatile material ideally suited for structural applications, offers unique advantages in drainage, ventilation, and safety. While its uses are broad, understanding the factors influencing its cost is crucial for optimizing both budget and project efficiency.
Firstly, material choice plays a pivotal role in determining cost. The most common materials for bar grating include carbon steel, aluminum, and stainless steel. Carbon steel tends to be the most economical option, providing robustness and flexibility for various environments. However, it requires proper maintenance to prevent rust. Stainless steel, often higher in price, offers superior resistance to oxidation and corrosion, making it ideal for harsh environmental conditions and applications requiring stringent hygiene standards, such as food processing plants. Aluminum, while typically in the mid-range of costs, provides excellent corrosion resistance with the added benefit of being lightweight, making it a feasible option for applications where weight savings are a priority.
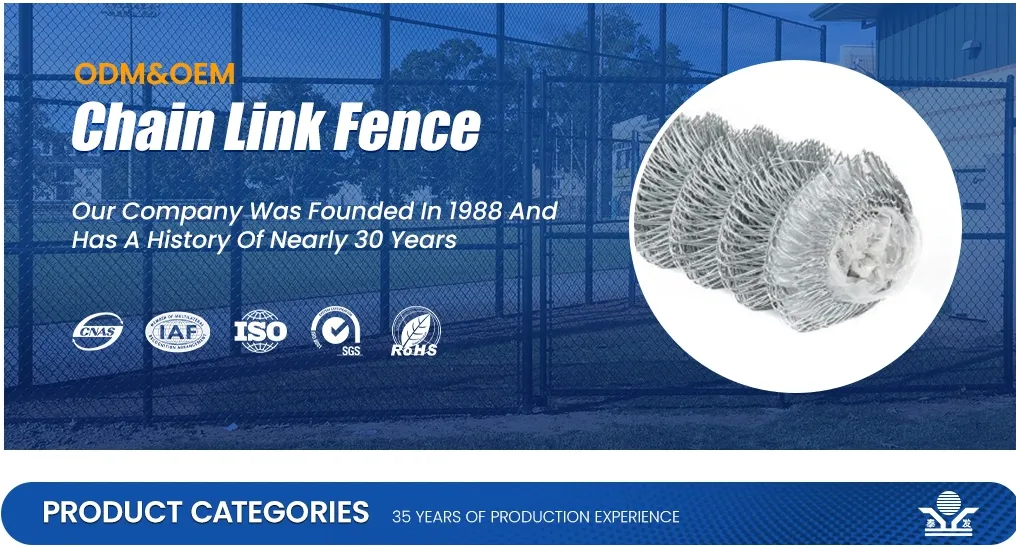
Manufacturing processes also significantly affect cost. Press-locked, swaged, and welded are the primary methods used in bar grating fabrication. Welded bar grating usually tops the list in strength and durability, involving the welding of cross bars to bearing bars to ensure a reliable product. While generally more costly, its resilience in challenging applications justifies the price. Swaged grating, prevalent in aluminum materials, involves mechanically locking bars together, typically offering a more cost-effective solution for light-duty applications.
Customizations in bar grating sizes and finishes further contribute to cost variation. Custom sizing is essential for projects with specific requirements, allowing optimal structural integrity and harmony with existing infrastructure. Finishes, ranging from galvanized coatings to painted surfaces, not only enhance aesthetics but also extend the lifespan of the material by adding layers of protection against elements.
bar grating cost
Volume and project scale cannot be overlooked when considering cost. Bulk purchases often afford discounts, underlining the importance of forecasting project needs accurately. Additionally, engaging with suppliers who understand your project's scale and specific needs often results in better pricing and product recommendations tailored to your demands.
Finally, logistics and regional economic factors can influence pricing structures. Geographic location impacts transportation and delivery costs, while market conditions, such as fluctuating raw material prices, can cause variations in pricing.
Establishing a relationship with a reliable supplier can enhance trustworthiness and streamline the procurement process. Reputable suppliers will not only offer competitive pricing but provide insightful consultancy to customize bar grating solutions for your specific application needs.
In conclusion, bar grating cost intricacies demand attention to detail and expert consultation. Whether you prioritize material quality, manufacturing process, customizations, or scale, understanding these components will empower you to make informed decisions that balance performance and budget. Rely on suppliers who demonstrate expertise and reliability, ensuring the selection of products that meet safety standards and long-term operational needs. By considering these factors, businesses can navigate the complexities of bar grating costs with confidence, striking that perfect balance between price and functionality.